Its been an ok start but I guess the pictures don't show all the drawings, searching, reading and trawling forums for the last 6 months to get to a point of something tangible on my dining room table even though its just a few bits of metal bolted together ! Actually when you finally decide on what to build and a scale that's only the beginning and a whole raft of decisions become apparent - motor size, realistic details or more functional, build materials, what you can actually build at home and what has to be outsourced, electronics ( I haven't even looked at this yet

) and hydraulics/actuators etc. Looking and reading others build threads have been the most help as they are slightly different in lots of ways and shows that you can achieve the same result by using different designs.
I have finally decided on a 1:14 scale although it was originally more a 1:16-18 size. I found that trying to build the tracks was a pain in the *** so brought some roller chain with attachments to shorten the process. This made me upscale to 1:14 to make things look the right size but somehow the roller chain didn't cut it for me in the looks department ( wanted more detail) and I switched back to home made links:
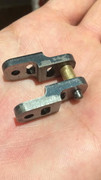
i decided to stick with the 1:14 scale as i had gone down that road to far already to turn back and plus the additional size made things easier to squeeze things inside and or make parts.
With the amount of time they take to produce, i am still worried that the tracks wont work properly somehow. I think i will just make one side complete with pads and run to make sure its all ok before continuing further. 3d printing is also a great help to make functional prototypes
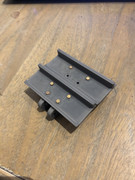
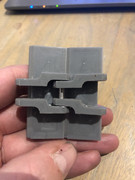
but without cnc, my manual milling abilities still has some variance that's not there on a 3d print ( still learning the milling operations as its my first mill)
Fusion 360 has been a revelation in the build and has helped me no end plan things out before spending time and money on possibly wasted parts. I purchased a 3d model and started scaling and drawings parts in fusion 360that I could use and make:
As my mill and lathe is on the smaller side, there is only some much time in the day to make parts so I decided to design parts in a sort of a layered manner to have someone laser cut the rough outlines for me to mill all the finishing touches and tolerances. I can then weld or bolt together the layers and grind/mill to shape.
For the mechanical moving parts and drive train i have been trying to utilise readily available parts like bushes, bearings and pins to minimise my machining time but still ended up making what seemed like a million 6 mm brass sleeves for my track pins
i love having to learn new skills to make parts I cant buy !
I am currently working on finishing one side of tracks ( tedious so i am trying to do 3 sets of links a day ) and breaking this up by working on the drive train design and internal mounts for the motors etc.
i do need some advice of the sprocket RPM etc but will put some questions together tomorrow and post
cheers for now
Rob